Dye-sublimation is a printing process used on many types of man-made fabrics to produce strikingly vivid graphics for large retail or commercial or exhibition purposes. This can be on banners, backdrops, flooring and signage.
This guide will help you to identify when and where to use large format dye-sublimation printing and the benefits and advantages of using this highly durable print technology
What is Dye-Sublimation Printing?
Dye-sublimation printing is a digital printing technology, also known as digital sublimation, or direct sublimation. It is a full-colour graphic print method most often used for signs, banners, fabrics and clothing – usually items with a sublimation-friendly (polymer-like) surface.
Using a mix of CMYK (cyan, magenta, yellow and black) colours dye-sublimation prints high density graphics directly onto man-made fabrics and textiles through a combination of heat and pressure. The transferred images become part of the substrate resulting in a permanent embedded image.

The Dye-Sublimation Printing Process
Dye-sublimation uses heat transfer technology to embed into the printed material. It follows a two-part process enabling the dye to be first transferred to a sublimation paper and secondly to be fixed to the substrate, fabric or print material:
Step 1
Sublimation dyes are transferred on sheets of high-release transfer paper using liquid gel ink.
Step 2
The transfer papers are then transferred from the paper onto the substrate material. The heat and pressure of the printing press ensures the dye penetrates the substrate, converting the dye into a gaseous form without a noticeable liquid form and producing a permanent and durable colour-bond. As the heat is removed the dye returns to solid state.
This process enables the dyes to be fused at the molecular level, and unlike screen printing it does not fade, crack or peel under everyday weathering conditions.
The Best Applications for Large Format Dye-Sublimation Printing
If the material substrate can receive a dye then it is suitable for sublimated printing. These materials can include:
Acrylic
Aluminium
Ceramics
Fibreglass
Glass
Plastic
However, because of the high heating processes involved (often in excess of 200 degrees Centigrade), substrate melting temperatures should always be consulted.
Dye-sublimation fabric printing
Fabrics like theatrical backdrops, flags and anything that can be made from PVC materials requiring flexibility, benefit greatly from dye-sublimation printing. Any fabrics prepared for sublimation are then able to allow even the softest and gentlest of print patterns to be displayed with both vibrancy and durability.
Dye-sublimation banner printing
Any exterior banners or signs made from polyester or PVC are ideal choices for dye-sublimation printing, allowing for photographic-quality prints to highlight corporate branding and retail signage.

Dye-Sublimation vs Inkjet Printing
Perhaps the biggest difference between inkjet and dye-sublimation printing is the heat processes involved. Very high temperatures are needed as the rollers press the dye from the transfer paper to the substrate. Whereas inkjet printers do not even get close to these kinds of temperatures.
Because of this the next big difference is the way sublimation allows the gaseous colour dyes to permeate into the surface of the substrate to become a permanent part of the surface. Inkjet inks cannot attain such permanent colour bonding. It allows sublimated prints to last significantly longer, in more hostile environments than inkjet prints.
However, the big drawback of dye-sublimation is that it cannot print onto many natural products without them first having a polymer coating to receive the dye.
When it comes to print quality inkjet technology is fast improving. While dye-sublimation can individually print colours in a continuous tone, ensuring a smooth, naturally photographic quality to the graphics, inkjet printing has advanced to be able to produce microscopic ink droplets to produce equally superior images.
Advantages and Disadvantages of Using Large Format Dye-Sublimation Printing
There are a number of advantages to be aware of when using dye-sublimation, most of which are due to the simple technology that it uses; for instance, dye-sublimation printers generally have fewer moving parts, meaning they are considered less likely to break down and can print over large surface areas at once.
No drying time
When printing on fabric the sublimation-dye process means it can be folded, worn or packed as soon as it leaves the printer without any of the usual smear risk of other print methods.
Mess-free/Fade-free
The ink isn’t stored as a liquid so there are no risks of spillage and because these dyes penetrate the print material it is less prone to fading. Furthermore, it will neither degrade plastic substrates or be a risk to running when exposed to water.
High fidelity graphics
Because of its continuous-tone technology every dot can be printed in a different colour. Dye-sublimated prints can have exceptionally high-resolution graphics and remain colour friendly for a very long time whilst maintaining photographic quality prints.
Small order friendly
While the energy requirements of dye-sublimation are smaller than other printers as (it uses no water) it’s unique ability to allow flexible customisation allows it to be quickly and easily set for small-batch orders and one-of-a-kind prints.
However, dye-sublimation isn’t the best choice for every print job. There are obviously going to be some disadvantages to consider:
Recycling and waste
There can be a lot of non-recycleable waste with dye-sublimation due to the two-part process it needs to transfer to the substrate. No other print process requires this two-step process and once used these transfer papers cannot be reused.
Limited substrate suitability
Sublimated printing isn’t ideal for some natural fibres like paper and work best on materials with a polymer coating.
Light vs dark
As the name suggests dye-sublimation works to ‘dye’ rather than ‘print’ on the substrate material. Therefore the use of lighter-coloured substrates naturally work with more visual success than darker materials.
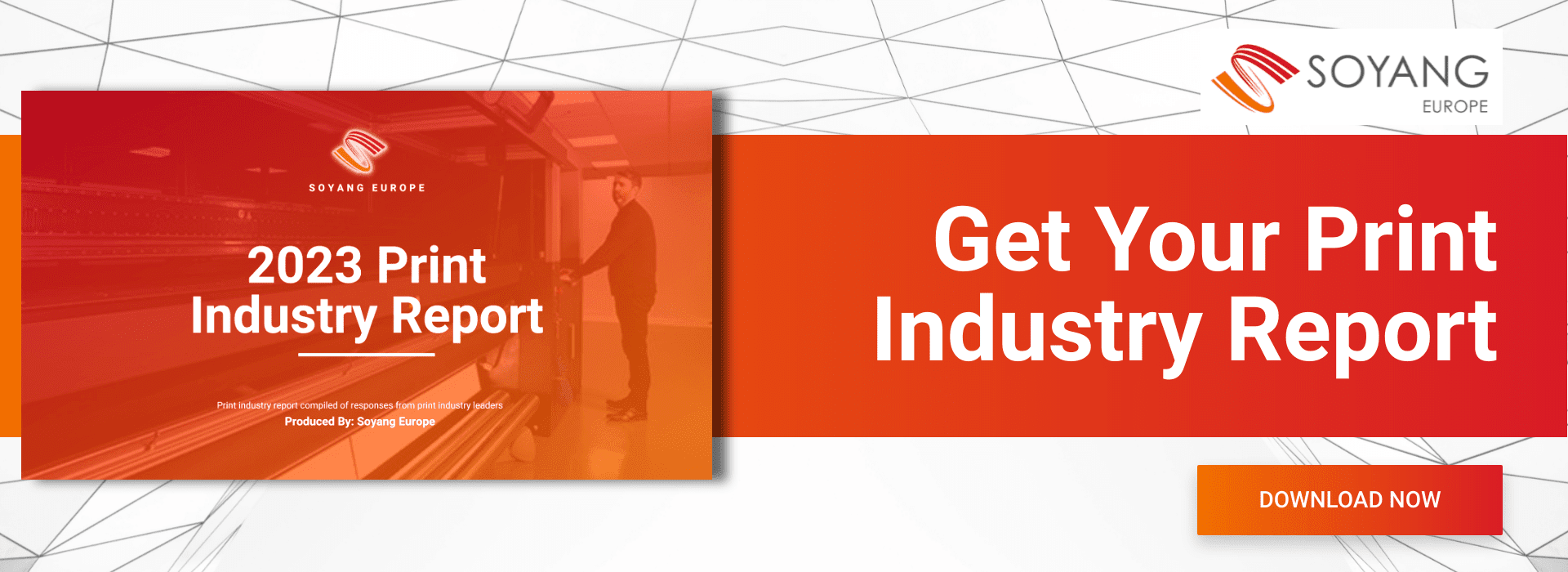