In the past, printing on fabrics and textiles was just about choosing the right size, style, and colour. These days, customers are a lot more conscious of their environmental footprint and are willing to look for brands that offer environmentally-friendly options, even if it means paying a little extra to support their beliefs.
This is a trend that we see in many industries already and there are eco-friendly options for just about everything we do these days.
So how does eco-friendly screen printing work and what do you need to do if you want to adopt these options in your business too?
There are two important components when it comes to screen printing; ink and blanks. The ink is what will transfer onto the fabric, and blank is a term used for the blank material that is ready to be printed on. By focusing on eco-friendly options for both the ink and blanks you use, you can expect to see a number of great advantages.
Plastisol inks are standard but not environmentally-friendly
In today’s screen printing industry, plastisol inks are the standard for most commercial printing operations. It’s made up of a chemical known as polyvinyl chloride (PVC) which is composed of a plasticizer liquid and PVC resin.
While PVC is praised for its versatility in many different applications, its production can release extremely harmful chemicals known as polychlorinated biphenyl (PCB) and dioxin. These are also carcinogenic according to the World Health Organization.
Although some work has been done to minimise the negative effects of plastisol inks, they are still relatively harmful compared to other alternatives available on the market.
Water-based inks are much more beneficial for the environment
Water-based inks are made of 100% biodegradable pigments in a water base. This makes it much safer to use in industrial applications and also screen printing. It’s surprisingly affordable given the advantages it offers, and it also offers high-quality printing without costing the environment.
Water-based inks are also much more gentle to the environment and can be safely washed away after use instead of requiring specialised tools and products to break it down like plastisol.
To summarise, here are the most important benefits of using water-based inks and why more printing companies should start using them in screen printing:
- 100% biodegradable and safer for the environment.
- Versatile and can be used to print on a variety of different items.
- Results in a softer print on the material.
- Will not “melt” when ironed over like plastisol inks.
- Much more vibrant colours.
- Extremely durable prints after proper curing.
- More comfortable to wear since the ink won’t weigh down the garment.
- Creates a more breathable garment since the ink penetrates the fabric.
- Makes cleaning and maintaining screen printing equipment much easier.
- Does not require specialist tools or products to wash away like plastisol.
As you can see, water-based inks come with a number of fantastic benefits. While being eco-friendly is a huge draw to water-based inks, there are a number of benefits that can also make it cheaper to run your screen printing business and the end product is often a much higher quality than those printed using plastisol inks.

Are there disadvantages to using water-based inks?
While there are plenty of advantages for water-based inks, there are a couple of reasons why it’s yet to see industry-wide adoption. We believe it’s important that printing businesses understand the pros and cons of water-based inks, so here are some of the minor downsides.
- May have trouble printing onto darker materials.
- Inks can sometimes be affected by the colour of the material.
- While versatile, there are some materials that may not work with water-based inks. For example, if you plan to print onto a dark material, it must be made from 100% cotton for water-based inks to show up.
Water-based inks are generally a great option for most use cases. For some specific cases, you may need to do a little more preparation. However, this isn’t much to ask for if you’re interested in swapping to eco screen printing.
In short, there are undoubtedly a few minor downsides to using water-based inks. However, you can overcome those issues by planning ahead, testing your prints, and ensuring that you’re using high-quality blanks.
Finding quality blanks to screenprint on
Lastly, you can consider using quality blanks to screen print on. Blanks are the second component in screen printing and there are many material choices to consider using. Most cheaper options are used as a standard in the industry, but these materials can be low-quality and their production methods may be harmful to the environment.
For example, you may want to consider using shirts made from bamboo. Bamboo shirts offer long-term freshness, they’re made from incredibly soft materials, and they’re excellent at regulating heat. They’re also resistant against UV radiation and are resistant to creasing even without ironing. To top it off, they’re eco-friendly and have minimal impact on global environmental concerns.
But even if you’d like to stick with a regular cotton shirt, there are still ways to ensure that your blanks are environmentally-friendly. For example, regular cotton is often grown by using harmful pesticides that can leach into the environment. This causes major damage to the surrounding earth and soil and makes it difficult for future generations to continue growing on that land. On the other hand, organic cotton is made using beneficial insects as a natural pesticide. This also strengthens the fibres, making them a lot stronger than conventional cotton.
Conclusion
So if you’re looking to make screen printing eco-friendly, it’s a good idea to consider changing the types of blanks you use and also swapping to a water-based ink. While there are other small ways to switch to eco-friendly screen printing, these two components made the biggest impact and your customers will be happy to hear that you’ve changed your methods.
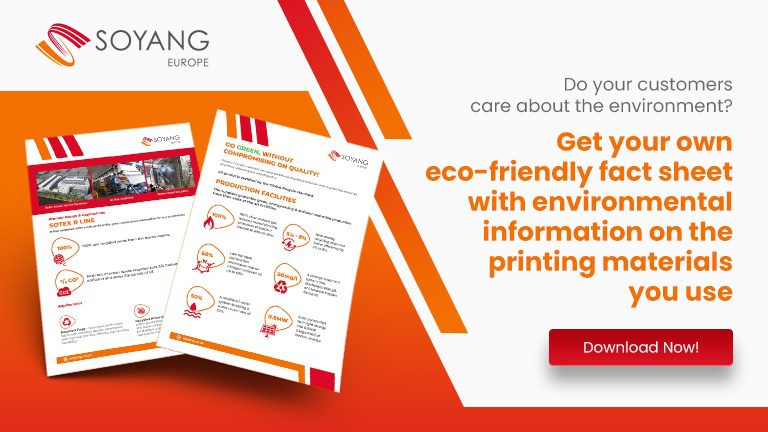