The print is done. It looks a million dollars. Now, you need to ensure it stays looking that way. Here’s the why, when and what of large format printing and laminating.
Benefits of large format printing laminating
There are lots of reasons why laminating large format print makes sense. These include:
UV protection
UV inevitably causes inks to fade. Even UV-resistant inks won’t last forever (although they’ll last much longer than non-UV resistant inks). Choose a laminate with added UV protection and you give your large format print a booster shot of protection which should further help protect it from fading.
General protection
Lamination makes large format print material thicker, more substantial and more robust. By its very nature, the effect of lamination is to place a protective layer over the print. Together, the result is large format print that’s less likely to crease or wrinkle and far harder to cut, rip, tear or otherwise damage.
Easy clean
Lamination makes cleaning easier, which means greasy fingers, dirt and smudges don’t get the chance to diminish the power of your print.
Special properties of large format printing laminating
It’s easy to think of laminate purely as a protective layer – but it can perform an active role in the task the print is asked to perform. The right laminate could create a writable and wipeable layer for audience interaction. It could bring anti-vandal properties to your print, so it gets the chance to make its impact for longer without being destroyed by graffiti. It could add an important non-slip layer to floor graphics.
Types of lamination in printing
There are really only two basic lamination types in printing: film and liquid, and two types of laminator: hot and cold. Let’s explore the latter element first.
Hot or cold, which laminator should you choose?
Cold laminators do their job through pressure, squeezing a clear adhesive film layer onto your print. Hot laminators, as the name suggests, add heat to the mix which melts the adhesive and helps to create a strong, durable bond between print and laminate.
That strength and durability makes hot lamination the default choice in many print applications providing the ink and material are both suitable for heat lamination. That may not be the case with, for example, some solvent or eco-solvent inks that use heat as part of the curing process.
Film or liquid lamination?
Film and liquid are the two main types of lamination in printing although there are numerous sub-categories of each lamination type.
Film laminate is the default option for all materials with a smooth surface.
Liquid laminates are the better choice for textured media where it would be impossible to ensure a complete seal when placing a film layer onto the print surface. Liquid lamination is ideal for canvas and PVC scrim banners, as the laminate won’t be compromised by the natural billowing, creasing and flexing of the banner.
The simplest way to select the right type of lamination for your printing?
Where you can, and subject to any requirements with ink, heat etc, match the laminate type to the print material (so, for example, match a PVC print with a PVC laminate). That way, you’ll ensure the base and laminate layer behave in the same way. This will reduce the chances of one layer shrinking or expanding at a faster rate than the other, which will keep your print looking as good as you intended.
Large format printing and laminating – When to laminate
You’ll probably be familiar with the various types of printing methods, but you may not know that your choice of print method can influence when you laminate.
As we explore in our guide to print banner options, solvent and eco-solvent inks penetrate large format print materials, effectively ‘tattooing’ the image onto the banner. That penetration is enabled by the solvent, which then evaporates leaving just the image behind.
The evaporation of the solvent is the curing process (you may have heard it referred to as ‘outgassing’). it takes time, so you should never laminate a solvent-based ink immediately as you’ll trap solvent beneath the laminate, which can lead to a ‘cloudy’ final product.
Most ink manufacturers recommend 24 hours of curing time before lamination. Depending on the ink, lamination type and material, you may be able to reduce that, but there should always be a generous break between printing and laminating.
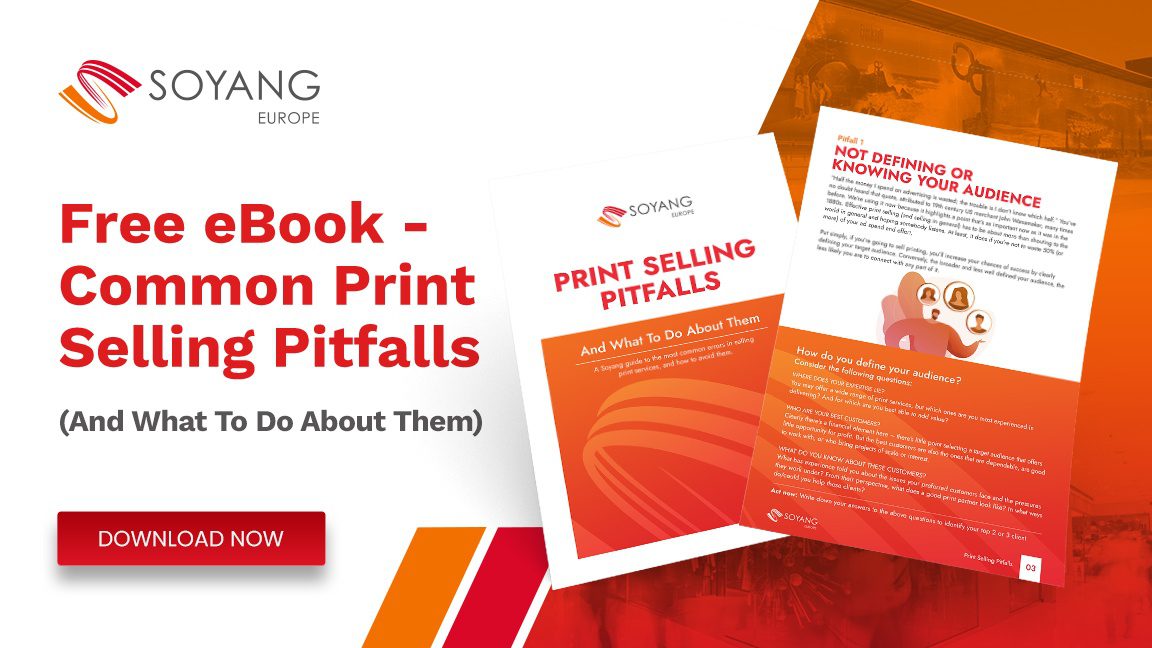